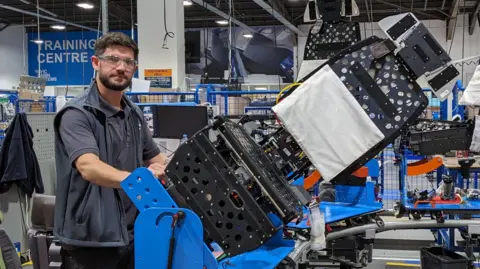
In a warehouse constructing in a quiet city in Northern Eire, a robotic arm is opening and shutting an airplane meal desk over and over.
It has been programmed to hold out this mundane process no fewer than 28,000 instances, day and evening, for greater than per week. And it gained’t even get a bag of peanuts.
“We will measure the pressure that the robotic’s having to use to that,” says Gerald King, head of engineering at Thompson Aero Seating in Banbridge. “Is it growing? Which suggests extra friction.”
Thompson makes top quality and enterprise class seats – the costly form often on the entrance of passenger plane, with their very own privacy-simulating enclosures, built-in leisure techniques, and heaps of leg room.
The corporate has numerous machines for testing the longevity and security of such seats. Together with a brand new £7.5m facility, opened final autumn, the place crash take a look at dummies are strapped to a seat and shot down a brief observe at unbelievable speeds.
The thought is to make sure that the seat – and passenger – would survive a short publicity to 16 g’s. It’s the solely facility of its form on the island of Eire.
Maybe surprisingly, just below one third of the world’s plane seats are manufactured in Northern Eire, in line with Make investments NI, an financial improvement company. Thompson, which was purchased by a Chinese language firm in 2016, is one of some companies within the area that specialise on this commerce. The agency at the moment churns out roughly 1,500 seats per 12 months.
One other main Northern Eire-based provider of seats is Collins Aerospace, in Kilkeel. There’s additionally Alice Blue Aero, in Craigavon.
One of many largest seat manufacturing firms worldwide is Safran. It has services on six continents.
However, because of the pandemic, demand for plane seats has flip-flopped dramatically of late. When Covid-19 emerged, the aerospace manufacturing business slowed to a crawl. Globally, firms laid off hundreds of employees. Thompson, for one, minimize its personal workforce in half, and has confronted monetary losses working to many hundreds of thousands.
The world has ultimately opened up once more, however seat producers haven’t been capable of finding all of the expert employees they want, that means that demand, globally talking, is outstripping provide. It’s a “very tough scenario”, Airbus’ chief government mentioned in June, referring to the sluggish provide of seats and different cabin components.
“The business misplaced that experience, each by way of direct, hands-on manufacturing, but additionally by way of educating youthful folks how you can do the job,” explains Nick Cunningham, an analyst at Company Companions who tracks the fortunes of one other seat maker, Safran.
One of many issues, he provides, is that seat makers are discovering it exhausting to get their seats examined and authorized rapidly by third-parties, since they’re additionally dealing with labour shortages.
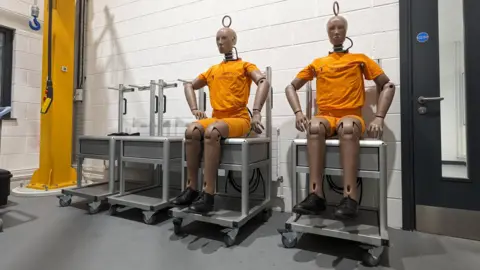
Thompson, nonetheless, can sidestep this drawback with its in-house testing services, explains Colm McEvoy, vice chairman of company accounts. He says that the agency is ready to meet its prospects’ wants at current, although he provides, “We’re having to be very strategic close to the brand new prospects.”
There are greater than 650 folks working at Thompson’s websites in Northern Eire, however, on the time of writing, the corporate had greater than a dozen job vacancies listed on its web site. “We’re in competitors with different manufacturing firms to attempt to safe one of the best expertise,” says Mr McEvoy.
Regardless of this problem, Thompson has a five-year plan to multiply its annual output of seats. Mr McEvoy reveals me across the manufacturing facility flooring on the agency’s Portadown web site, the place employees are busy riveting aluminium seat components collectively, and checking the advanced wiring for the leisure techniques in these costly buildings – every seat prices “tens of hundreds” to make, says Mr McEvoy.
“This seat in entrance of you is probably the most advanced seat we make,” provides Eoin Murray, operations supervisor. It takes round 100 hours for the extremely expert employees right here to assemble in full.
Mr Murray is set to spice up the speed of manufacturing on this manufacturing facility flooring. He reveals off a jig, developed in-house, upon which a seat could be mounted and angled in order that employees can simply entry the perimeters or underside. “This permits us to hit like a fee 14,” says Mr Murray – 14 seats produced in a single shift. “I must get to 18. To twenty,” he provides.
To that finish, there’s one other much more succesful model of the jig within the room subsequent door, a prototype that employees right here hope will probably be even higher. Mr Murray and his colleagues are additionally growing new working practices – equivalent to utility belts with instruments organized within the sequence they’re required.
If the employee is left-handed, that sequence could be reversed in order that the method of selecting a device and finishing up a process with it’s as speedy as potential.
Staff right here rehearse and hone key phases of seat meeting, which helps them go sooner. A bit like studying how you can construct the identical piece of Ikea furnishings over and over till it turns into like muscle reminiscence, I recommend – simply much more sophisticated.
“We will seamlessly slot folks in, and so they can now work via these totally different phases with no computer systems,” says Mr Murray. “Once I began working right here, for those who advised me I might be working with out a pc I’d have advised you [that] you had been loopy.”
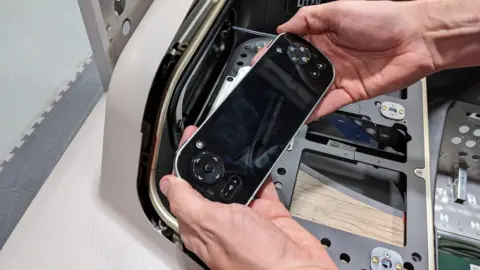
Moreover quantity, there’s fixed strain to provide you with new and higher seat designs, says Mr McEvoy. Airways need the most recent and finest leisure know-how, for instance – 32 inch screens at the moment are included in Thompson’s high seats.
“They’re striving for one thing totally different, one thing that makes them distinctive,” Mr McEvoy provides. Thompson makes use of leather-based and delicate materials on chosen components of the seat and enclosure to supply a luxurious really feel, which is more and more standard with airways. The seats themselves can recline into two-metre lengthy, totally flat beds.
One I attempt for myself is definitely snug – although I might most likely need to lie in it for seven hours or so to check it correctly, I believe to myself.
“They’re good corporations, very, superb corporations – they know what they’re doing,” says Marisa Garcia, an aviation business analyst who used to work in seat manufacturing herself, referring to the Northern Eire-based firms who make plane seats. She has no business relationship with any of them, she provides.
Regardless of provide chain complications, seat producers are in a very good place to wash up, in the event that they show themselves capable of hold tempo with business necessities, says Ms Garcia: “The demand is there from passengers – and the demand is there from airways.”